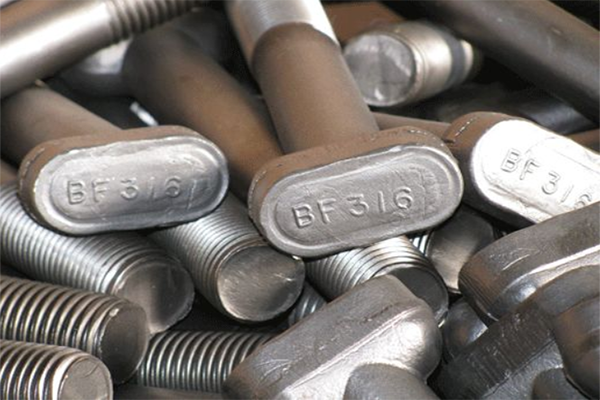
One of the great things about stainless steel fasteners is the intrinsic protection within the makeup of the steel. The fastener maintains a shiny, clean finish (when electropolished) while maintaining corrosion resistance. Let’s get into the meaning of stainless steel, its characteristics, and the differences in Type 304 and 316.
What Makes Stainless Steel Fasteners “Stainless?”
The term stainless steel is used for a family of iron-based alloys that contain at minimum 10.5% chromium. This amount of chromium allows for corrosion and heat resistance due to the creation of a surface layer that prevents oxygen from penetrating the steel. Rust cannot form, thus making it “stainless.” Often, their composition also includes other alloys such as nickel, manganese, sulfur, or titanium. These alloys add extra corrosion resistance.
In the fastener world, most stainless steel is austenitic stainless steel, commonly referred to as the 300 series. While there are many compositions that fall under the 300 series, we mostly use types 304 and 316. While they both provide excellent corrosion resistance and have similar compositions, their differences lie in the ratio of chromium to nickel and the environments they are used in.
Stainless Steel: Type 304
You will often hear the term “18-8” when researching the 304 series of stainless steel fasteners. 18-8 refers to the 18% chromium and 8% nickel in the steel. While many stainless materials in the 300 series have this 18-8 mixture, their chemistries and corrosion resistance do not necessarily meet that of type 304. Type 304 is the most popular of the 300 series of stainless steel, as it provides some of the best corrosion resistance in the series.
Stainless Steel: Type 316
Type 316 stainless steel fasteners fall right behind Type 304 in terms of popularity and provides excellent corrosion resistance. Unlike 304, Type 316 does not follow the 18-8 makeup. The chromium is lowered to 16% and the nickel is raised to 10%. Type 316 also contains 2% of molybdenum. Adding molybdenum provides superior resistance to chlorides which can cause pitting.
Because of its composition, Type 316 is used in more corrosive environments where the fasteners will be exposed to chemicals, solvents, or salt water. Type 316 stainless steel fasteners are best used in applications with abrasive chemicals or direct salt spray.